新能源汽車大型壓鑄件尺寸精度研究
2025-6-26 來源:重慶賽力斯新能源汽車設計院有限公司 作者: 林真廷 葉小軍
【摘要】: 賽力斯汽車推出具有地面最強悍性能的 SUV 問界 M9,其車身結構采用了先進的一體化壓鑄全鋁底盤,有效減輕了簧下質量,進而提升了操控性能,然而壓鑄件尺寸精度如何控制成為行業最大的難題。提出了一種在生產過程中針對壓鑄工藝過程、免熱處理材料、校型工裝設備、過程管控及壓機參數調試等方面優化的控制策略,這一策略不僅有助于提升新能源汽車的制造水平,同時也為壓鑄行業的發展提供了有益的參考和借鑒。
【關鍵詞】: 一體式壓鑄工藝 ; 鋁合金后車體 ;免熱處理材料 ; 尺寸精度
隨著 “雙碳” 目標的實施,全球汽車行業對節能環保的重視程度日益提升。為實現節能減排,各國紛紛認可并支持新能源汽車的發展。在這一背景下,新能源車企為滿足消費者對輕量化、高效能的需求,不斷加大研發和生產投入。一體化壓鑄技術,以其在生產效率、成本降低和減重方面的顯著優勢,正成為新能源車身結構發展的關鍵技術。特斯拉、蔚來、小鵬等領先新能源車企已積極布局一體化壓鑄領域,預示著壓鑄機將逐步取代焊接機器人,成為新能源汽車制造的核心裝備。該技術的核心在于大型壓鑄機的卓越性能、創新的免熱處理材料配方、精密的壓鑄模設計以及優化的壓鑄工藝參數。特別是鋁合金一體化壓鑄技術,其輕量化和高效生產的特性使其成為新能源車企的標配技術。本文旨在深入探討一體化壓鑄技術在新能源汽車制造中的后車體尺寸精度控制運用。
壓鑄工藝介紹
1.壓鑄定義
壓鑄 ( High Pressure Die Casting ,HPDC),是高壓鑄造的簡稱,是指將熔融的液態金屬或半固態金屬以較大的壓力(20~120MPa)和速度(20~100m/s )壓入模具型腔,并使之在較高的外部壓力作用下凝固的成型工藝。在壓鑄過程中,金屬液能夠快速的充滿模具型腔,在外部壓力作用下,不僅能夠保持金屬液與模具型腔尺寸和形狀的一致性,而且在模具型腔的強冷作用下,外部壓力使得金屬液與模具緊貼,從而使鑄件 - 模具作為整體具有優異的散熱性,使金屬液在極短的時間內完成凝固,獲得晶粒細小、組織均勻的鑄件。
一體化壓鑄,是指將傳統的多個單獨、分散的小件進行重新設計高度集成,在利用大型壓鑄機進行一次成型,省略焊接的過程直接得到一個完整的大型件的新型壓鑄工藝。壓鑄島如圖 1 所示。
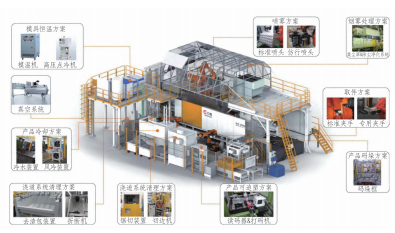
圖 1 壓鑄島
2.傳統壓鑄與一體壓鑄的區別
(1)材料選擇 傳統壓鑄工藝所使用的的鋁合金發展起步較早,材料的工藝特性相對成熟可控。傳統鑄造結構件因其尺寸較小,在鑄造成型后還可進行 T6、T7 熱處理,以提高零件的力學性能及耐腐蝕性。常用 ADC12、ADC14、A360、A380、ENAC-43400、ENAC-4600 及 SF36(AlSi10MnMg)。
一體化壓鑄件由于尺寸較大,形狀復雜,熱處理帶來的熱脹冷縮可能會引起零件的尺寸變化和表面裂紋等缺陷。因此需選用免熱處理的鋁合金材料。材料同時還需具有高強韌性、高流動性、高的連接包容性等性能特點。常用 C611、560 合金、A152。
(2)模具 傳統壓鑄由于傳統鑄件尺寸較小,結構相對簡單,模具設計中的分模方案,澆注系統,排氣系統,頂出系統,模溫系統的設置較為簡單。且在模具設計前期計算冗余度設定較高,模具后期進行試模調整也更加方便。
一體化壓鑄模具結構尺寸更大,結構也更為復雜。這對模具設計中的澆鑄系統,模溫系統,頂出系統以及真空度的設置有更高的要求。在前期設計時需進行充分的模擬分析,風險評估,以減輕模具后續調整難度。在模具材料選取和機械加工工程中,也要充分考慮模具的壽命和可靠性。
(3)設備 傳統壓鑄工藝由于零件尺寸較小,開模方向的投影面積較小,鑄造過程中所需的鎖模力不大。對壓鑄機的性能要求不會太高,所需噸位一般不超過 4500t,壓鑄島配套設備尺寸、數量都較小。
一體化壓鑄件整合集成了多個小件,所以其重量和開模方向的投影面積相比于傳統壓鑄零件增大不少,對壓鑄機的鎖模力噸位也提出了更高的要求。目前市面上用于一體化壓鑄成型的壓鑄機噸位一般不會低于 6000t,周邊設備尺寸、數量也相應增加。
(4)工藝 傳統壓鑄工藝人們主要依靠經驗來做出判斷和決策,過往的壓鑄從業人員將其經驗匯總成經驗公式或者是經驗圖表,供行業
參考。
一體化壓鑄可以參考的類似產品較少,且許多工藝參數都突破了傳統壓鑄的工藝參數上限,傳統經驗公式是否有效還需進一步驗證。為保證鑄件的成型質量,對壓鑄合金的純凈度,噴涂材料的低發氣性,沖型前型腔真空度都有更高的工藝要求。
(5)用途 傳統壓鑄汽車領域主要適用于電動機外殼、變速器外殼、電控外殼殼體類零件。一體壓鑄主要應用于扭力梁、前艙總成、后地板及側圍 CD 柱內板等車身輕量化部件。
3.一體壓鑄后車體制造工藝
(1)制造工藝 一體壓鑄后車體生產過程是一個精密而復雜的工藝流程,它涉及多個關鍵步驟,從毛坯壓鑄開始,一直到裝配標件并檢測合格交付產品。壓鑄工藝是一體壓鑄后車體生產過程中的關鍵環節,它涉及將熔融的金屬注入模具中,通過高壓和冷卻使其凝固成所需形狀。在壓鑄前,要準備好模具,模具的精度和質量直接影響到最終產品的品質。模具的制造需要依據產品的設計圖樣,經過精密加工而成。
毛胚壓鑄首先需要調整壓鑄機的參數,如壓力、速度、溫度等,以適應不同產品的生產需求。接著,壓鑄機通過高壓將熔融的金屬以壓入模具中,并使其充滿模具的每一個角落。這個過程需要嚴格控制時間和壓力,以確保金屬能夠充分凝固并達到所需的密度和強度。如圖 2 所示。
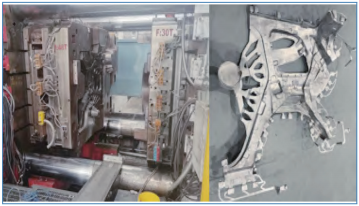
圖 2 毛胚壓鑄
毛胚鑄件表面可能還附有一些多余的金屬或毛刺,需要進行切水口和打磨等處理。接下來是毛坯校型,通過對鑄件進行精確的測量和調整,使其符合產品設計的尺寸和形狀要求。如圖3所示。
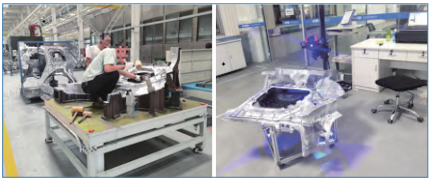
圖 3 毛坯校型 圖 4 藍光掃描
最后,通過藍光掃描技術,可以快速、準確地獲取產品的三維數據,并與設計數據進行比對分析。這種檢查方式不僅提高了檢測效率,更能發現肉眼難以察覺的微小缺陷,從而確保產品質量的穩定性和可靠性。如圖 4 所示。
總的來說,一體壓鑄后車體生產過程中的壓鑄工藝是一個復雜而精細的過程,它涉及多個環節和步驟,需要嚴格控制每一個細節,以確保最終產品的質量和性能達到要求。隨著技術的不斷進步和工藝的不斷優化,一體壓鑄技術將在汽車制造等領域發揮越來越重要的作用。
尺寸精度控制方案
1.材料選擇
為減少大型鑄件熱處理后的變形,當前主要方法是研發免熱處理材料。在汽車結構件領域,研究集中于 Al-Si 系和 Al-Mg 系鋁合金。這些材料通過添加化學元素和優化壓鑄條件,形成細小晶粒,實現與傳統材料相當的力學性能。主流材料包括 C611(美國鋁業公司)和 SF36(德國萊恩金屬),它們已廣泛應用于汽車結構件生產,如蔚來 CD 柱和奧迪 A8 車身。這些材料在特定工藝下具有出色的延伸率,適用于多種車身部件。C611 和 SF36 化學成分以及力學性能見表 1、表 2。
表 1 壓鑄鋁合金各元素質量分數 (單位 :%)

表 2 壓鑄鋁合金拉伸力學性能要求

2.校型工裝設備
(1)定位基準 校型工裝定位選擇如圖5所示,A1~A4作為基準目標,限制Z向移動以及繞Y軸、X 軸轉動的三個自由度 ; 選擇 B 孔作為主定位孔,限制 X 向以及 Y 向移動的兩個自由度 ; 選擇 C 孔作為次定位孔,限制繞 Y 軸的轉動。
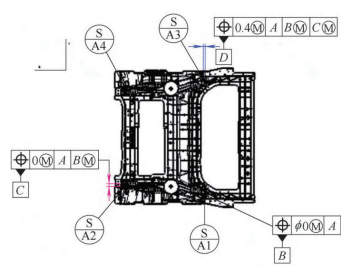
圖 5 一體式后車體 GD&T 圖樣
(2)校形工裝 切邊整形模指利用沖模修邊工序件的多余邊緣廢料,使其具有一定高度、直徑和形狀的沖壓模具。切邊模主要用于修整拉申的邊緣,讓端面平整美觀,確保零件的一致性便于下一步裝配。如圖 6 所示。
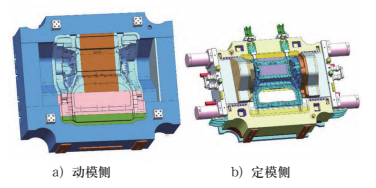
圖 6 壓鑄模具
通過 RPS 點將零件定位在校形檢具上,針對需要控制的形狀、尺寸及位置進行校形,使零件滿足尺寸精度要求。
3.過程管控
(1)藍光掃描 分別對毛坯校型、機加(面、孔)及成品校型后進行掃描測量,并針對掃描的結果進行反饋,以便提前識別問題點提前規避尺寸缺陷。
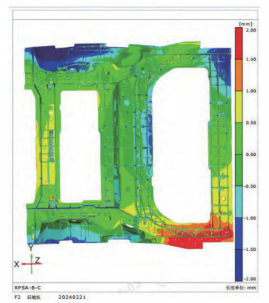
圖 7 成品校形掃描結果
如圖 7 所示,可以看出綠色部分 ±0.5mm為合格區域,紅色及藍色分別為 ±2mm 偏差區域,根據圖示可以看出兩邊輪罩區域及前部與門檻梁搭接區域存在嚴重超差情況。
(2)成品檢具測量 成品檢具作為零件合格交付前的最后一道檢測關卡,在尺寸精度把控方面起到至關重要的作用。為減少工作量提高工作效率,針對不同零件可以進行關鍵點位選取制作為如圖 8 所示測量記錄表進行百分之百監控測量。
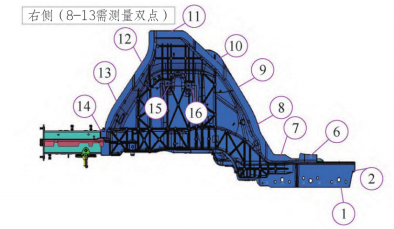
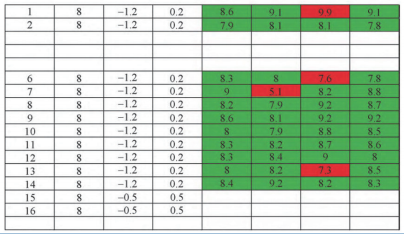
圖 8 關鍵測點檢測工藝卡
4.壓機參數調試
1)壓力 : 壓射比壓常規設置為 30~90MPa,增壓比壓一般設置在 50~300MPa。
2)速度 : 低階段速度為 0.1~0.5m/s; 高速階段速度為 3~6m/s; 內澆口速度為30~60m/s。
3)時間 : 充填時間由壓鑄件體積、平均厚度,填充速度決定,薄壁件一般不超過 0.1s; 持壓時間薄壁件 1~2s,厚壁件 3~5s; 留模時間主要由產品尺寸結構和工藝溫度決定。
4)溫度 : 澆注溫度通常由定量爐內金屬液溫度表示,一般為 700~740℃ ; 預熱模具溫度一般為150~180℃,連續工作溫度一般為180~220℃。
改進前后對比分析
通過材料選擇、校型工裝設備、過程管控及壓機參數調試四個方面,壓鑄件整體尺寸精度質量均有較高提升,結合改進前后一體式后車體進行抽樣測量并做分析,得出以下結論。
選取測量點 6~14 號,結合統計分析軟件Minitab 通過雙樣本對比分析,具體見表 3~ 表 5。
表 3 描述統計量
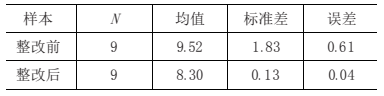
表 4 差值的估計值

表 5 檢驗值

方法 :μ1 為整改前的總體均值 ;μ2 為整改后的總體均值 ; 差值 μ1 - μ2 已針對此分析假定了
等方差。
原假設 :H0=μ1 - μ2=0
備擇假設 :H1=μ1 - μ2 > 0
由分析結果可知差值下限為 0.153 >假設差值 0,同時 P 值為 0.032 < 0.05,充分證明原假設被拒絕,備擇假設成立,整改后改善明顯。充分證明選擇最優的材料,通過校型工裝百分之百校正,通過過程管控及壓機參數調試,最終能明顯提高壓鑄件尺寸精度。
結語
中小型一體壓鑄結構件在車上的應用方面已經成熟,大型一體壓鑄后車體工藝結構設計任然是技術難點,需要車身設計與工藝技術人員緊密協作共同開發。從制造工藝角度看,目前壓鑄機和模具等主要工藝裝備已具備配套條件,可支撐投影面積 20000cm2鑄件的開發,C611 和 SF36的免熱處理材料已在部分鑄件上生產試用,具備配套條件。壓鑄件尺寸精度也可通過工裝定位、面熱處理材料、校型工裝、壓機參數調試及過程管控確保外觀尺寸一致性。
投稿箱:
如果您有機床行業、企業相關新聞稿件發表,或進行資訊合作,歡迎聯系本網編輯部, 郵箱:skjcsc@vip.sina.com
如果您有機床行業、企業相關新聞稿件發表,或進行資訊合作,歡迎聯系本網編輯部, 郵箱:skjcsc@vip.sina.com
更多相關信息