普通車床加工細長軸的工藝探究
2020-5-14 來源: 中石化江鉆石油機械有限公司 作者:何青青
摘要:在普通長車床上加工細長軸零件時,由于長度和直徑的比值較大,在軸向和徑向切削力的作用下很容易造成細長軸零件彎曲變形與振動,加工中對操作者的技術水平要求很高。雖然目前我公司在加工細長軸方面已實現了批量加工的能力,但是加工精度和生產效率方面暫且滿足不了實際需求,因此解決普通車床上加工細長軸外圓的難題就顯得尤為重要。通過分析細長軸加工過程中產生變形的原因,合理調整裝夾方式和加工參數,設計新工裝,優化加工方法來提高加工效率,并且保證較高的加工質量,為細長軸零件的大批量生產提供技術支持。
關鍵詞:細長軸;車削工藝;變形原因;加工方法
1、 概述
在機械加工中,長度與直徑之比大于 25(L/d>25)的軸稱為細長軸。這類零件在卡爪夾持力、切削力、重力和頂尖軸向力的作用下,加工過程中很容易產生外圓表面粗糙度低和彎曲的問題。因此,解決細長軸的加工精度和加工效率的問題,就是控制加工過程中零件的受力及受熱變形的問題。
2、 細長軸車削的工藝特性
2.1 工件剛性很差,若卡爪、中心架和頂尖三個部位裝夾不合適,受自由度的限制,易在軸向切削力、徑向切削力及重力的作用下彎曲變形,從而產生細長軸的振動,直接影響加工精度和加工效率。
2.2 工件散熱性能差,加工中產生較大的切削熱而彎曲變形。
2.3 工件加工中通常經歷粗車、半精車和精車的過程,單次切削時間長,刀具、工件冷卻不及時、工件切削余量不均對刀具損耗大,易產生竹節狀的幾何形狀。
2.4 工件加工過程中,中心架子支撐外圓的圓周跳動量和表面精度低,直接影響中心架的裝夾。
2.5 工件加工過程前,由于中心架兩個下支承滾輪的支撐力和一個上壓緊輪壓力調整不當,也會影響加工精度。
3 、細長軸加工中彎曲變形的原因
通常,裝夾細長軸零件原材料的方式有兩種,一種是“一夾一頂”的方式;另一種是兩頂尖支撐的方式。我們根據設備特性,主要分析“一夾一頂”的裝夾方式。如圖 1 所示。
3.1 切削力導致的變形
外圓加工過程中,切削力可以分解為軸向力 PX、徑向力 PY及切向力 PZ。三種切削力對工件產生彎曲變形的影響是不同的。
3.1.1 軸向削力 PX的影響
軸向切削力平行作用在軸線方向上。由于細長軸的剛性較差,軸向切削力 PX作用在工件外圓面上,會以頂尖為支點對工件形成一個扭矩。當軸向切削力超過工件屈服強度時,便產生
縱向彎曲變形。如圖 1 所示。
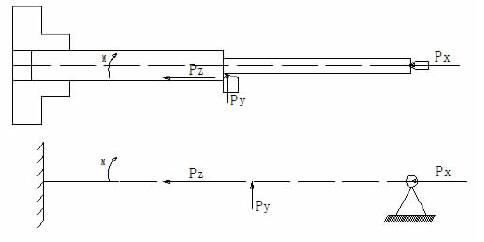
圖 1 軸向切削力 PX受力示意圖
3.1.2 徑向力 PY的影響
徑向切削力 PY是垂直作用工件軸向方向上。由于細長軸的剛性較差,徑向會以卡爪和頂尖為支點將工件頂彎。同樣,當徑向切削力超過工件屈服強度時,亦會生彎曲變形。如圖產 2 所示。
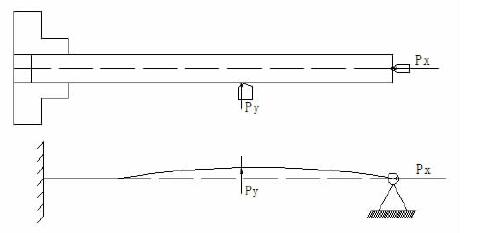
圖 2 徑向切削力 PY受力示意圖
3.2 切削熱產生的影響
由于加工過程中,卡盤和頂尖都是固定不動的,因此兩者之間的距離也是固定不變的。切削中產生的切削熱會造成工件熱伸長,工件受到 X 向自由度的限制產生軸向擠壓,從而產生彎曲變形。
4、 解決細長軸加工受力和熱變形的措施
4.1 優化工件裝夾方法減少過定位受力
我單位在加工細長軸前,通常采用“一夾一頂”的裝夾方式。主軸卡爪一般用 2~3 個牙齒長度夾緊工件一端,,另一端使用頂尖固定預先加工好的頂尖孔,以確保工件能在同一軸線上自由旋轉。若卡爪裝夾工件過長產生過定位、加工前頂尖對頂尖孔的預緊力過大,車削時工件受熱伸長,以及機床長時間使用,造成主軸端軸心與頂尖軸心產生不同軸,均會導致細長軸受到過定位和軸向擠壓力的作用彎曲變形。為解決此問題,我們在采用“一夾一頂”裝夾方式時,在卡爪端與細長軸之間墊入一個開口鋼絲圈,減少卡爪與工件接觸長度,消除安裝時的過定位。如圖 3 所示。
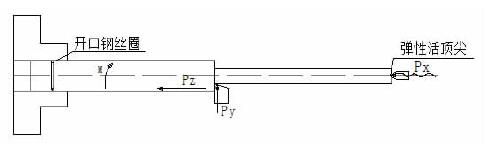
圖 3 一夾一頂裝夾的改進
4.2 優化工件車削剛性穩定切削力
在加工細長軸外圓時,可使用中心架輔助支撐來增加工件剛性。一般加工細長軸使用中心架的方法有:
4.2.1 用中心架支承車細長軸
為增加工件車削時的剛性就需要降低細長軸長徑比,通常將中心架支承在工件中段,對細長軸外圓進行分段車削。在使用中心架之前,必須在工件中間車出一段 40~70mm 長,用于中心架頂頭體支承的“架子口”。加工出的架子口表面粗糙度及圓柱度需要以打表的方式控制在 0.04mm 以內;其次,車削時,中心架的頂頭體滾輪或支承爪與工件架子口的接觸面需加潤滑油保持潤滑。特別是支承爪的支承方式時,可以在支承爪與工件架子口之間加一層砂布或研磨劑進行研磨抱合,確保良好的接觸,以滿足細長軸外圓的加工精度。如圖 4 所示。
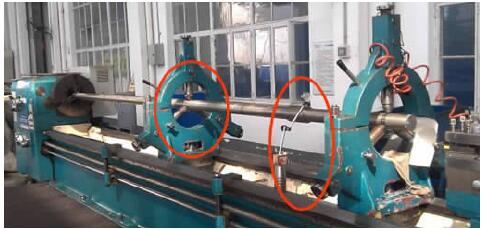
圖 4 中心架支撐工件
4.2.2 用定心套筒支承車細長軸
實際加工中,我們還會受到原材料直線度的影響,工件兩側切削量不同,會造成架子口尺寸和產品尺寸難以取舍。為了解決這個問題,我們設計制作定心套筒工裝輔助加工。定心套筒工裝的設計思路是:a.在工件中段以“虛擬四爪卡盤”的方式減少工件長徑比,降低車削架子口的繁瑣性;b.加工一套外圓精度較高、熱處理硬度適中、壁厚能強度要求的空心殼體;c.殼體長200~250mm,殼體內徑較工件外徑大 30mm 左右,外徑不得大于中心架使用范圍;d. 在定心套筒工裝兩端距離端面 30mm 左右處,等分安裝四個 M16 的螺栓。
使用步驟是:a.吊裝工件前將定心套筒放置于工件中部,同時將八只螺栓預緊于工件,確保定心套筒與工件的間隙大體一致;b.使用“一夾一頂”的方式裝夾工件;c.用吸附于小刀架上的磁力百分表,分別在定心套筒兩端進行徑向和軸向打表,調整并擰緊螺栓,確保徑向和軸向誤差≤0.05mm;d.移動中心架至定子套筒中間部位,調整上下頂頭體讓滾輪與定心套筒外圓緊密接觸,隨即可實施車削加工。
4.2.3 用跟刀架支承車細長軸
跟刀架是一種固定在床鞍上,可以跟隨車刀移動,支承工件重力、抵消徑向切削力 PY、增加工件的剛度的機床附帶工裝,通常有兩爪和三爪兩種。從而提高細長軸的形狀精度和表面粗糙度。使用兩爪跟刀架時,工件自身重力以及車刀給工件的切削抗力 PY,使工件貼住跟刀架的兩個支承爪上,這類跟刀架的弊端是半閉合支撐。工件在旋轉切削時可能因原材料硬度不均,切削抗力的變化導致工件瞬時離開支承爪而產生跳動;使用三爪跟刀架時,工件受到三個支承塊的限制和切削抗力的作用,工件在 Y、Z 向自由度受限,車削時不易產生振動。因此,選用三爪跟刀架車細長軸至關重要。如圖 5 所示。
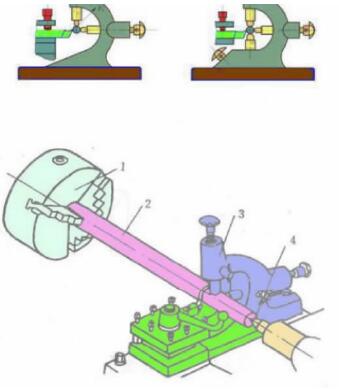
圖 5 跟刀架使用示意圖
4.3 減少工件的熱變形伸長
熱伸長量公式如下:△L=a L△t (1)式(1)中:a———材料線膨脹系數(1/℃);L———工件的總長(mm);△t- 工件升高的溫度(℃)。
例:車削直徑為 120mm,長度為 5000mm 的馬達轉子,材料為 45# 鋼,車削時因受切削熱的影響,工件由原來的 15℃上升到 55℃,求這根細長軸的熱變形伸長量?

從式(2)計算可知,我公司這類產品所屬的細長軸熱變形伸長量較大。同時,裝夾中工件受到卡爪和頂尖的限位,工件無法自由伸長,因而產生彎曲。為此,我們采取以下措施:
(1)使用彈性回轉頂尖,可有效減少工件熱變形伸長。
(2)加注充分的切削液,減少工件的溫升而引起熱變形。
(3)刀具保持鋒利,降低車刀與工件的摩擦熱。
5、 細長軸加工中常出現的問題和解決辦法
5.1 用中心架輔助分段加工細長軸,經常出現工件外圓銜接不好的問題如何解決?
細長軸分段車削過程中,需每加工 100mm 長度即對外圓直徑實施測量,隨時調整中心架頂頭體緊固程度,始終保證工件軸線與主軸軸線同軸,要求細長軸外圓尺寸控制在±0.02mm 以內。中心架一端外圓完成車削后將工件卸下,調頭重新裝夾車另一端或移動定心套筒工裝至已加工面重新找正繼續車削。由于細長軸分段車削是在兩次裝夾中完成的,常因操作不當造成外圓銜接處過渡部圓滑。因此,應注意以下事項:先調整中心架下方兩個頂頭體,使其與工件外圓接觸。調節支撐力度過大不但會頂彎工件,還會使頂頭體支承爪和工件之間摩擦增大,導致工件摩擦熱過大從而變形;調節支撐力度過小,中心架無法發揮作用,工件在車削時會產生跳動。直接的判斷方式分兩種:一種是低速轉速打表找正,一種是中速旋轉進刀預刮削工件一圈,觀察工件表面刀痕均勻性。調整好中心架兩個支撐頂頭體后,扣上蓋并調整壓緊端頂頭體,判斷其力度的方式與兩個支撐頂頭體相同。
細長軸車削過程中,需隨時觀察頂頭體與工件的接觸和磨損情況并及時調整,同時時刻在接觸面添加潤滑油或油基潤滑液降低磨損。
5.2 用跟刀架輔助車削細長軸時,外圓表面產生的“竹節形”如何解決?所謂“竹節形”是車削的外圓尺寸忽大忽小,不均勻。用跟刀架輔助車削細長軸,分析“竹節形”形成的原因:反向切削過程中,跟刀架支撐爪調整的預緊力過大,此時車削點靠近工件尾端且工件剛性好、工件受到頂尖的約束,可按初定的進刀量正常車削出所需的外徑。車削一段長度后工件剛度逐漸下降,跟刀架支撐爪也逐步釋放壓緊力,將工件壓向車刀,造成吃刀量增大,導致軸外徑縮小;隨后,當跟刀架支撐爪跟到尺寸縮小的軸外徑時,支撐爪向外壓向工件的力度降低,車削抗力將工件壓向支撐爪,造成吃刀量減小,導致軸外徑增大。隨后這樣有規律的變形,直接造成軸外圓表面加工成了“竹節形”。具體解決方法有:
調整跟刀架卡爪與工作接觸壓力,直至正常用力無法擰動調節旋鈕。調整單刀切削量在 1.5mm 以內和進給速度,降低工件切削抗力。使用彈性頂尖,減少工件變形產生的彎曲形變。
6 、結論
由于細長軸自身剛性差,外圓車削時候的受力和受熱對加工質量和效率產生很大影響。所以,熟悉產品的正確裝夾和優化加工方法,可保證細長軸的加工質量。
投稿箱:
如果您有機床行業、企業相關新聞稿件發表,或進行資訊合作,歡迎聯系本網編輯部, 郵箱:skjcsc@vip.sina.com
如果您有機床行業、企業相關新聞稿件發表,或進行資訊合作,歡迎聯系本網編輯部, 郵箱:skjcsc@vip.sina.com
更多相關信息